Modern Hydraulic System Parts Guide
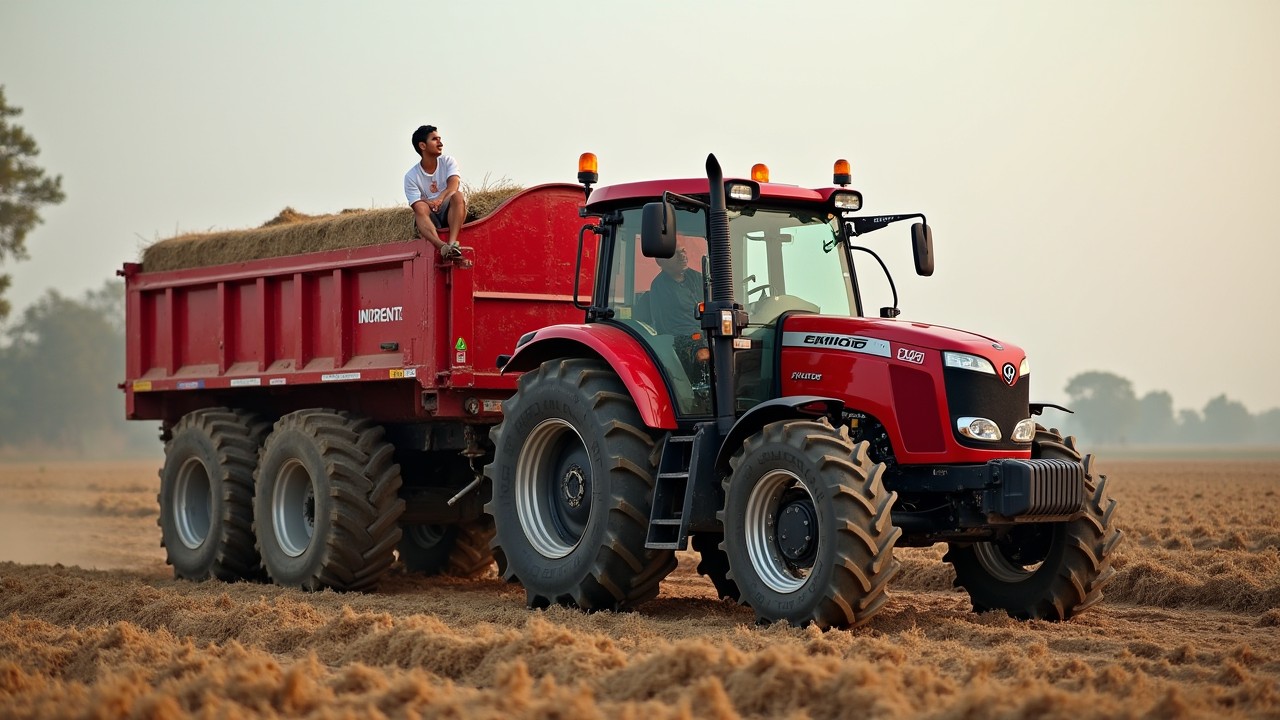
Introduction
Understanding Tractor Hydraulic Parts and Their Importance
Tractor hydraulic parts are critical components that power essential functions such as steering, lifting, braking, and transmission in modern agricultural machinery. Hydraulic systems use fluid power to perform heavy-duty tasks with precision and efficiency. These systems rely on a combination of hydraulic pumps, cylinders, valves, hoses, and filters to convert mechanical power into hydraulic energy, ensuring smooth and reliable operation. Understanding the key hydraulic parts, their functions, and maintenance requirements is crucial for optimizing tractor performance, reducing downtime, and extending the lifespan of your machinery. This guide provides a comprehensive overview of modern tractor hydraulic parts, helping you make informed decisions for efficient farming operations.
Hydraulic Pumps: The Powerhouse of Tractor Hydraulic Systems
Hydraulic pumps are the heart of the tractor’s hydraulic system, responsible for generating hydraulic pressure that powers all functions. They convert mechanical energy from the engine into hydraulic energy, supplying pressurized fluid to hydraulic cylinders and motors. There are several types of hydraulic pumps used in tractors, including gear pumps, piston pumps, and vane pumps. Gear pumps are known for their simplicity and reliability, making them ideal for basic hydraulic systems. Piston pumps offer high-pressure performance and efficiency, suitable for heavy-duty applications. Vane pumps provide smooth flow and are commonly used in steering systems. Regular maintenance, including checking fluid levels and inspecting seals, ensures optimal pump performance and prevents costly breakdowns.
Hydraulic Cylinders: Driving Linear Motion and Force
Hydraulic Hoses and Fittings: Ensuring Secure Connections and Fluid Flow
Hydraulic hoses and fittings play a vital role in transporting hydraulic fluid between components. They are designed to withstand high pressure and harsh environmental conditions. High-quality hydraulic hoses are made from reinforced rubber or thermoplastic materials to ensure durability and flexibility. Fittings are used to connect hoses to pumps, valves, and cylinders, providing leak-proof and secure connections. It’s essential to choose the right size and type of fittings to prevent pressure loss and leakage. Regular inspection for cracks, wear, and leaks ensures safe and efficient hydraulic system operation. Proper maintenance of hydraulic hoses and fittings prevents contamination, improves fluid flow, and reduces the risk of system failure.
Hydraulic Filters: Protecting the System from Contaminants
Aftermarket parts are usually cheaper than OEM components, which can be appealing for cost-conscious buyers. However, their lack of precise engineering and varying quality standards can lHydraulic Reservoirs: Storing and Maintaining Fluid Levelsead to frequent replacements and performance issues in the long run.
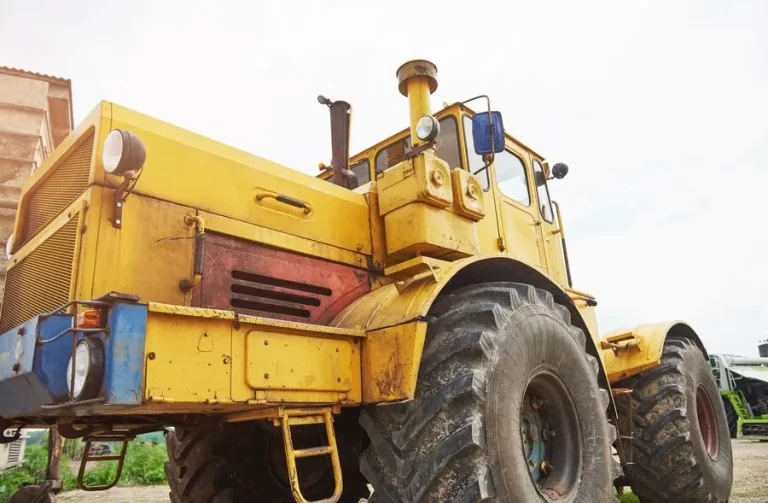
Hydraulic Reservoirs: Storing and Maintaining Fluid Levels
Hydraulic Braking Systems: Ensuring Safety and Control
Hydraulic braking systems provide powerful and reliable stopping force, ensuring safety and control in heavy-duty tractors. These systems use hydraulic pressure to activate brake pads or shoes, converting hydraulic energy into mechanical force. Key components of hydraulic braking systems include master cylinders, brake calipers, brake lines, and hydraulic fluid reservoirs. Regular inspection of brake pads, fluid levels, and hydraulic lines ensures safe and efficient braking performance. Replacing worn-out parts and maintaining the correct fluid viscosity enhance braking reliability and prevent accidents, ensuring the safety of operators and equipment.
Hydraulic Power Take-Off (PTO) Systems: Powering Attachments and Implements
Hydraulic Power Take-Off (PTO) systems are essential for powering attachments and implements such as plows, mowers, and loaders. They use hydraulic pressure to transmit power from the tractor’s engine to external equipment. PTO systems include hydraulic pumps, shafts, couplings, and control valves. Regular inspection and maintenance of PTO components ensure efficient power transfer and reliable operation. Lubrication of moving parts, checking hydraulic fluid levels, and ensuring secure connections prevent wear and improve PTO performance. By maintaining hydraulic PTO systems, farmers can maximize productivity and operational efficiency.
Hydraulic Power Take-Off (PTO) Systems: Powering Attachments and Implements
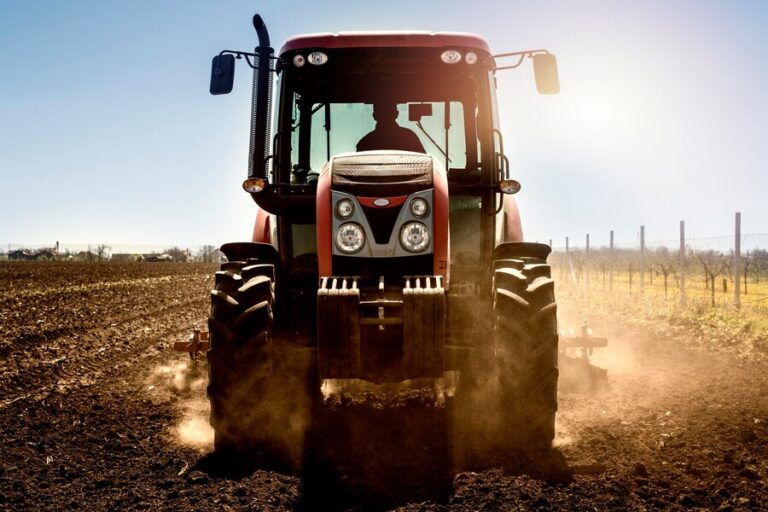
Hydraulic Cylinders: Driving Linear Motion and Force
Hydraulic pumps are the heart of the tractor’s hydraulic system, responsible for generating hydraulic pressure that powers all functions. They convert mechanical energy from the engine into hydraulic energy, supplying pressurized fluid to hydraulic cylinders and motors. There are several types of hydraulic pumps used in tractors, including gear pumps, piston pumps, and vane pumps. Gear pumps are known for their simplicity and reliability, making them ideal for basic hydraulic systems. Piston pumps offer high-pressure performance and efficiency, suitable for heavy-duty applications. Vane pumps provide smooth flow and are commonly used in steering systems. Regular maintenance, including checking fluid levels and inspecting seals, ensures optimal pump performance and prevents costly breakdowns.
How Hydraulic Systems Work: The Science Behind Fluid Power in Tractors
Hydraulic systems operate on the principle of fluid power, using pressurized hydraulic fluid to transmit force and motion. At the heart of the system is the hydraulic pump, which converts mechanical energy from the engine into hydraulic energy. The pump pressurizes the fluid, which then flows through hoses and valves to hydraulic cylinders and motors. Hydraulic cylinders convert this fluid pressure into linear motion, enabling lifting, lowering, and pushing tasks. Meanwhile, hydraulic motors convert pressure into rotational motion, powering wheels, augers, and other rotating machinery. Valves control the direction, pressure, and flow of hydraulic fluid, allowing precise movement and speed control. The fluid is then returned to the reservoir, where it is cooled, filtered, and recirculated. This closed-loop system ensures efficient power transfer and consistent performance. Understanding the science behind hydraulic systems helps operators and technicians diagnose issues, optimize efficiency, and maintain safe operations.
Applications and Use Cases
When to Choose OEM Parts
OEM parts are ideal for essential repairs, particularly for critical systems such as the engine, transmission, or hydraulic systems. They are also recommended for newer tractors still under warranty, as using OEM parts helps maintain warranty coverage.
When Aftermarket Parts May Be Suitable
Aftermarket parts can be a practical choice for older tractors or non-essential components, such as exterior panels or minor accessories. However, careful consideration should be given to their quality and fit.
Hydraulic Pumps: Generating Power and Pressure for Tractor Functions
Hydraulic Valves: Controlling Direction, Pressure, and Flow in Hydraulic Systems
Hydraulic valves are critical components that control the direction, pressure, and flow of hydraulic fluid within the system. They determine how much fluid goes where, at what pressure, and in which direction, ensuring precise movement and operational safety. There are several types of hydraulic valves used in tractors, including directional control valves, pressure relief valves, flow control valves, and check valves. Directional control valves manage the flow direction to actuators, enabling forward, reverse, and neutral positions. Pressure relief valves protect the system from overpressure, preventing damage and ensuring safety. Flow control valves regulate fluid flow rates, optimizing speed and efficiency. Check valves allow unidirectional flow, preventing backflow and contamination. Proper maintenance of hydraulic valves includes cleaning, inspecting for wear and tear, and replacing damaged seals. Regular valve maintenance ensures accurate control, consistent performance, and extended system longevity.
Hydraulic Motors: Driving Rotational Motion and Powering Attachments
Hydraulic motors are dynamic actuators that convert hydraulic pressure into rotational motion, powering various attachments and implements such as augers, mowers, and conveyors. They are used in applications requiring continuous or variable speed rotation, delivering consistent torque and power. There are three main types of hydraulic motors: gear motors, vane motors, and piston motors. Gear motors are simple and reliable, providing consistent speed and torque. Vane motors offer smooth and quiet operation, ideal for steering systems. Piston motors are highly efficient and capable of handling high pressures, making them suitable for heavy-duty applications. Hydraulic motors are used in a wide range of agricultural machinery, including combine harvesters, balers, and sprayers. Proper maintenance, including checking fluid levels, inspecting seals and bearings, and replacing worn-out components, ensures optimal motor performance and prevents costly breakdowns. Regular maintenance also enhances efficiency and prolongs the life of hydraulic motors, maximizing productivity and profitability.
Conclusion
Modern tractor hydraulic parts are at the heart of today’s agricultural machinery, enabling precise control, powerful motion, and efficient energy transfer. From powering heavy-duty attachments to ensuring smooth steering and safe braking, hydraulic systems play an indispensable role in enhancing productivity and operational efficiency. As farming practices continue to evolve with advancements in technology, understanding the components, functions, and maintenance of hydraulic parts becomes more crucial than ever. By investing in high-quality hydraulic pumps, cylinders, valves, motors, hoses, and filters, farmers and agricultural professionals can optimize equipment performance, minimize downtime, and reduce operational costs.
One of the key benefits of modern hydraulic systems is their ability to perform complex tasks with precision and speed. Whether it’s variable-rate spraying, automated steering, or power take-off (PTO) operations, hydraulic systems offer unmatched versatility and control. With the integration of electronic sensors and computer-controlled actuators, today’s hydraulic systems deliver accurate and responsive movement, enhancing productivity and safety. Moreover, the adaptability of hydraulic systems to different attachments and implements makes them ideal for multifunctional tractors, ensuring year-round usability across various farming activities.
However, achieving optimal performance requires diligent maintenance and proper care of hydraulic parts. Regular inspection, cleaning, lubrication, and timely replacement of worn-out components prevent leaks, contamination, and system failures. Using the right hydraulic fluid, maintaining correct pressure levels, and following manufacturer guidelines are essential for preventing corrosion, overheating, and excessive wear. Implementing a proactive maintenance schedule not only enhances hydraulic efficiency but also extends the lifespan of the entire tractor system.